SMT貼片加工工藝包括哪些步驟?
單面組裝
原料檢測->絲印焊膏(點膠貼片)->貼片->烘干(固化)->回流焊接->清洗->檢測->返修
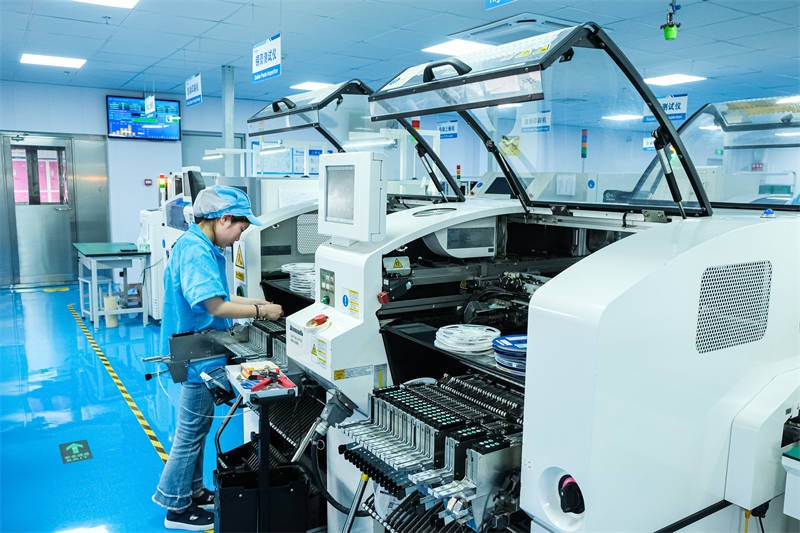
兩面組裝
A:進行原材料檢測=>點貼片膠在PCB的A面上的焊膏=>點貼片膠在貼片PCB的B面上的焊膏=>進行貼片工藝=>進行烘干=>進行回流焊接(最好只對B面進行)=>進行清洗=>進行檢測=>如有問題進行返修。
B:開始進行來料檢測=>檢測PCB的A面絲印焊膏(點貼片膠)=>將貼片固定在A面上=>進行烘干(以便固化)=>進行A面回流焊接=>清洗處理=>將板子翻轉=開始處理PCB的B面點貼片膠=>將貼片固定在B面上=>進行固化處理=>進行B面波峰焊接=>再次進行清洗處理=>進行檢測=>如有需要進行返修處理)
這個工藝適用于PCB的頂面采用回流焊、底面采用波峰焊的情況。對于底面組裝的表面貼裝器件(SMD),只有引腳數(shù)少于等于28的SOT或SOIC器件,才應該使用這個工藝。
單面混放工藝是一種在半導體制造中常用的工藝。它主要用于生產(chǎn)高密度電路板和集成電路。這種工藝將不同類型的元件或材料放置在電路板的一側,從而實現(xiàn)多種功能和連接。使用單面混放工藝,可以降低制造成本,提高生產(chǎn)效率,并滿足多種設計需求。
生產(chǎn)流程為:來料檢測->PCB的A面絲印焊膏(點貼片膠)->貼片->烘干(固化)->回流焊接->清洗->插件->波峰焊->清洗->檢測->返修。
混合工藝雙面放置
A:進行來料檢測,檢查PCB的B面的點貼片膠,然后進行貼片,待膠固化后翻板,接著插入PCB的A面插件,進行波峰焊接,然后清洗,再進行檢測,若有問題則進行返修。
適用于SMD元件超過分離器件的情況,先貼后插。
B:來料檢測-->PCB的A面插件(引腳彎曲)-->翻轉-->PCB的B面點貼片膠-->貼片-->固化-->翻轉-->波峰焊-->清洗-->檢測-->返修
適用于SMD器件以外的分離元件,先插后貼的方法非常實用。
來料檢測:開始檢測所收到的材料。
PCB的A面絲印焊膏:在PCB的A面上涂上絲印焊膏。
貼片:將元器件粘貼到PCB上。
烘干:將PCB放入烘干設備進行干燥。
回流焊接:通過回流焊機對元器件進行焊接。
插件,引腳打彎:對插件元器件的引腳進行彎曲。
翻板:將PCB翻轉到另一面。
PCB的B面點貼片膠:在PCB的B面點上貼片膠。
貼片:將元器件粘貼到PCB上。
固化:將貼片膠進行固化。
翻板:將PCB翻轉到原來的一面。
波峰焊:通過波峰焊機對貼片進行焊接。
清洗:對焊接后的PCB進行清洗。
檢測:對清洗后的PCB進行檢測。
返修A面混放,B面貼片:修復A面混放和B面貼片的問題。
D:來料檢測→PCB的B面點膠貼片→貼片→固化→翻板→PCB的A面絲印焊膏→貼片→A面回流焊接→插件→B面波峰焊→清洗→檢測→返修A面混放,B面貼片。先貼兩面SMD,回流焊接,后插裝,波峰焊。
E:來料檢測→PCB的B面絲印焊膏(點膠貼片)→貼片→烘干(固化)→回流焊接→翻板→PCB的A面絲印焊膏→貼片→烘干=回流焊接1(可采取局部焊接)→插件→波峰焊2(如插裝元件少,可使用手工焊接)→清洗→檢測→返修A面貼片、B面混放。
雙面裝配技術
A:對于來料檢測工藝流程而言,首先需要對PCB的A面進行以下步驟:檢測絲印焊膏的點貼片膠情況,進行貼片工藝,進行烘干以進行固化,進行A面回流焊接,隨后進行清洗,最后需要翻板。
對于PCB的B面,則需要進行以下步驟:檢測絲印焊膏的點貼片膠情況,進行貼片工藝,進行烘干以進行固化,最好僅對B面進行回流焊接,隨后需要進行清洗、檢測,并進行返修(如果有需要的話)。
這個工藝適用于在印刷電路板(PCB)的兩面都要安裝較大的表面貼裝器件,例如PLCC等。
B:進行來料檢測,檢驗PCB的A面絲印焊膏(點貼片膠)的質量,并進行貼片、烘干(固化)、A面回流焊接的工藝步驟。然后進行清洗,然后翻轉板面。對于PCB的B面,先進行點貼片膠、貼片、固化的工序,然后進行B面波峰焊接、清洗、檢測,最后進行返修工作。這一工藝方法適用于在PCB的A面進行回流焊接。