1.檢查印刷電路板上的電路圖和器件布局,確保沒有錯(cuò)誤或漏印。
2.檢查印刷電路板上的焊盤和元件之間的連接。如果發(fā)現(xiàn)有焊接不良或未連接的情況,需要重新焊接或修復(fù)。
3.檢查元件的方向和位置是否正確。如果發(fā)現(xiàn)錯(cuò)誤的方向或位置,需要重新安裝或調(diào)整。
4.檢查所有的元件是否正確對(duì)齊并與印刷電路板的焊盤對(duì)齊。如果發(fā)現(xiàn)有元件偏位或未對(duì)齊的情況,需要重新調(diào)整位置。
5.檢查印刷電路板上的引腳和元件之間的間距。如果發(fā)現(xiàn)間距過小或過大的情況,需要調(diào)整焊盤的大小或重新設(shè)計(jì)印刷電路板。
6.檢查印刷電路板上的引腳和元件之間的距離。如果發(fā)現(xiàn)距離過近或過遠(yuǎn)的情況,需要進(jìn)行適當(dāng)?shù)恼{(diào)整。
以上是處理SMT貼片加工印刷故障的方法。希望能對(duì)您有所幫助。
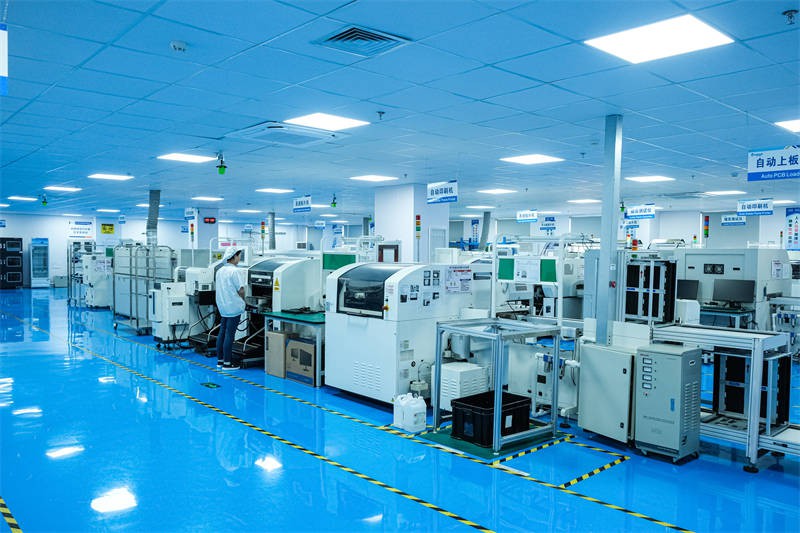
電子生產(chǎn)行業(yè)常用的SMT貼片加工存在許多常見故障。數(shù)據(jù)顯示,60%的故障源于錫膏印刷問題。因此,焊錫膏印刷的高質(zhì)量是確保SMT貼片加工質(zhì)量的重要前提。以下是小編為您提供的處理印刷故障的方法解釋。
SMT貼片加工是一種電子零部件的制造方法,它能將各種元器件直接粘貼在電路板表面上,而無需傳統(tǒng)的焊接方法。這種加工方式可以提高生產(chǎn)效率、降低成本,并且能夠?qū)崿F(xiàn)更小、更輕、更高密度的電子產(chǎn)品設(shè)計(jì)。在SMT貼片加工過程中,元器件會(huì)通過粘貼機(jī)和熱熔膠給設(shè)備表面粘貼上。然后,在回流爐中進(jìn)行熔化和焊接固定,最終得到成品。SMT貼片加工在電子制造領(lǐng)域得到了廣泛應(yīng)用,因?yàn)樗軌驖M足現(xiàn)代電子產(chǎn)品對(duì)于高性能、高可靠性和高集成度的要求。
1.“觸碰打印”是一種鋼網(wǎng)與PCB印刷方法的緊密結(jié)合,兩者之間沒有間隙。這種方法要求構(gòu)造具有穩(wěn)定性,適用于高精度的錫膏印刷。印刷完成后,鋼網(wǎng)和印制板保持平滑的手感,并與PCB分離。因此,該方法具有較高的印刷精度,特別適用于細(xì)小間隙和超微距離焊膏印刷。
印刷速率
隨著刮板的推動(dòng),焊膏能夠快速地在鋼網(wǎng)上滾動(dòng)前進(jìn)。較快的印刷速度對(duì)鋼網(wǎng)有益。
這種回彈現(xiàn)象不僅會(huì)造成焊膏的漏印,還會(huì)降低印刷速率。由于速率過慢,漿體無法在鋼網(wǎng)上流動(dòng),導(dǎo)致印刷到焊層上的焊錫膏分辨率低,通常是由于印刷速率太低造成的間隔過細(xì)。
比例尺設(shè)定為10×20mm/s.
鏟運(yùn)機(jī)有多種類型:
有兩種類型的鏟運(yùn)機(jī):塑料鏟運(yùn)機(jī)和鋼制鏟運(yùn)機(jī)。對(duì)于距離不超過0.5毫米的集成電路(IC),建議選用鋼制刮板,這樣在印刷后能更好地形成錫膏。
印刷方法:
常見的SMT貼片加工印刷方法有兩種,分別是觸碰印刷和非接觸式印刷。其中,非接觸式印刷是一種在鋼絲網(wǎng)印刷和印刷線路板之間留有空隙的印刷方法。這種方法的間隙一般為0.5×1.0毫米,適用于各種粘度的錫膏。在非接觸式印刷中,焊錫膏被刮板推入鋼網(wǎng)的開口,并接觸到印刷線路板上的印刷墊。然后,慢慢地移除刮板,將鋼絲網(wǎng)與印刷線路板分離。這種方法的好處在于降低了真空泄漏對(duì)鋼絲網(wǎng)的污染風(fēng)險(xiǎn)。
刮調(diào)節(jié)
刮刀操作點(diǎn)沿著45°方向進(jìn)行打印,可以明顯改進(jìn)焊膏在不同鋼網(wǎng)上打孔時(shí)的不均衡情況,同時(shí)還能減少對(duì)薄鋼網(wǎng)打孔時(shí)的損傷。刮刀的施加壓力通常為30N/mm。
為了避免焊膏因?yàn)镮C的安裝高度較低而塌陷,并在回流過程中出現(xiàn)短路現(xiàn)象,選取安裝高度時(shí)必須保持間隔不超過0.5mm,或者選擇0間隔或0~-0.1mm安裝高度。
再熔焊
造成安裝失效的主要原因是使用了再流焊。
1.溫度升高的速度太快了;
2.加熱溫度過高;
3.錫膏的加熱速度較線路板快。
4.通量的濕潤速度太快了。
所以,在確定再熔焊參數(shù)之前,必須充分考慮各個(gè)方面的因素,以確保在分批安裝之前焊接質(zhì)量沒有問題。